Shell cordovan is one of the world’s finest leathers. Historical records indicate that its origin dates back to Spain in the 7th century, specifically to the city of Cordoba where it was first made by the Visigoths. During the Moorish occupation of the Iberian Peninsula that followed, Cordoba became a renowned leather working centre. This is why this particular leather is known as Cordovan.
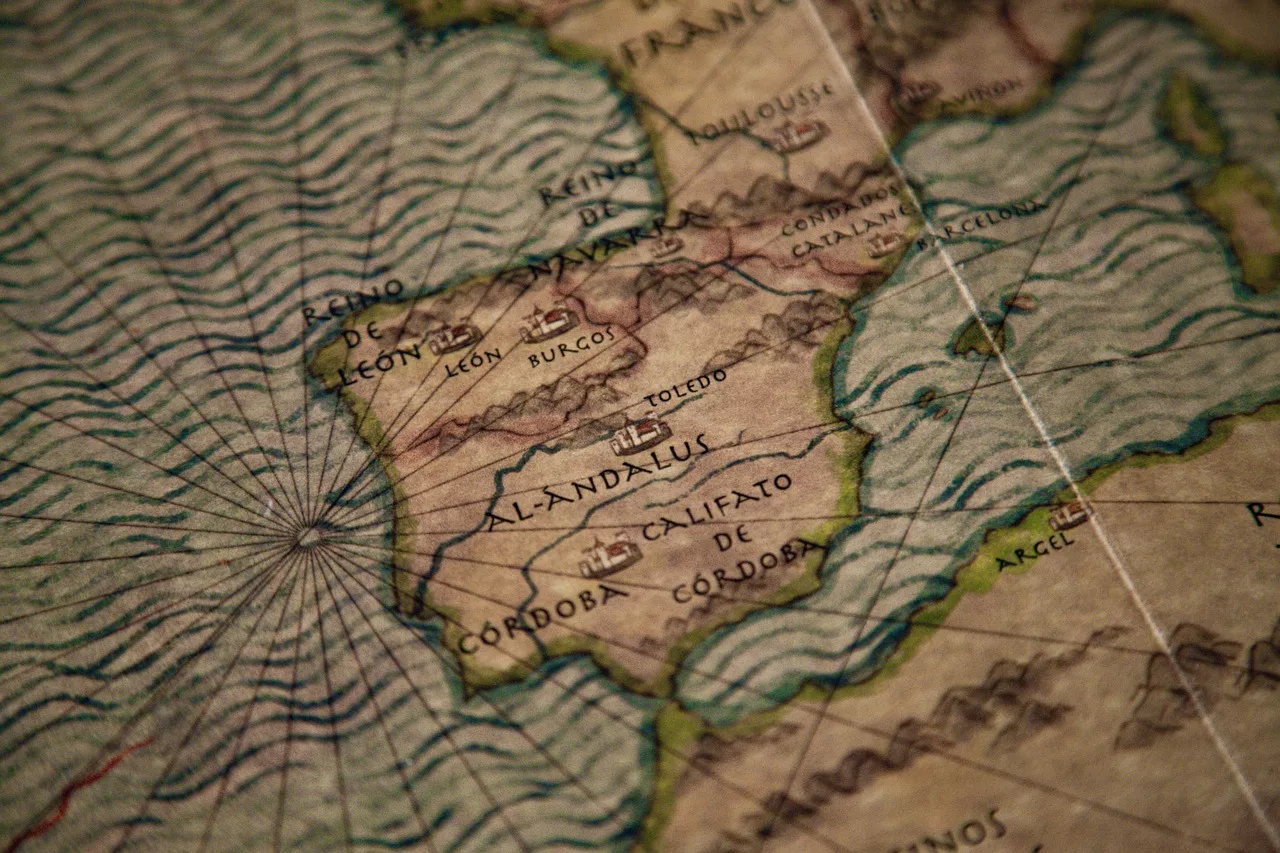
It comes from the fibrous connective tissue, known as the shell, found beneath the hide on the rump of a horse. This type of leather has a unique and super dense fibre structure, and lacks the pebbled effect of hides derived from other animal skin.
Since shell cordovan is labour-intensive to produce and comes from a limited supply of horse hides, its cost reflects its rarity and craftsmanship. A square foot is typically priced at around 100 USD, but it can go even higher depending on the supplier and the finish.
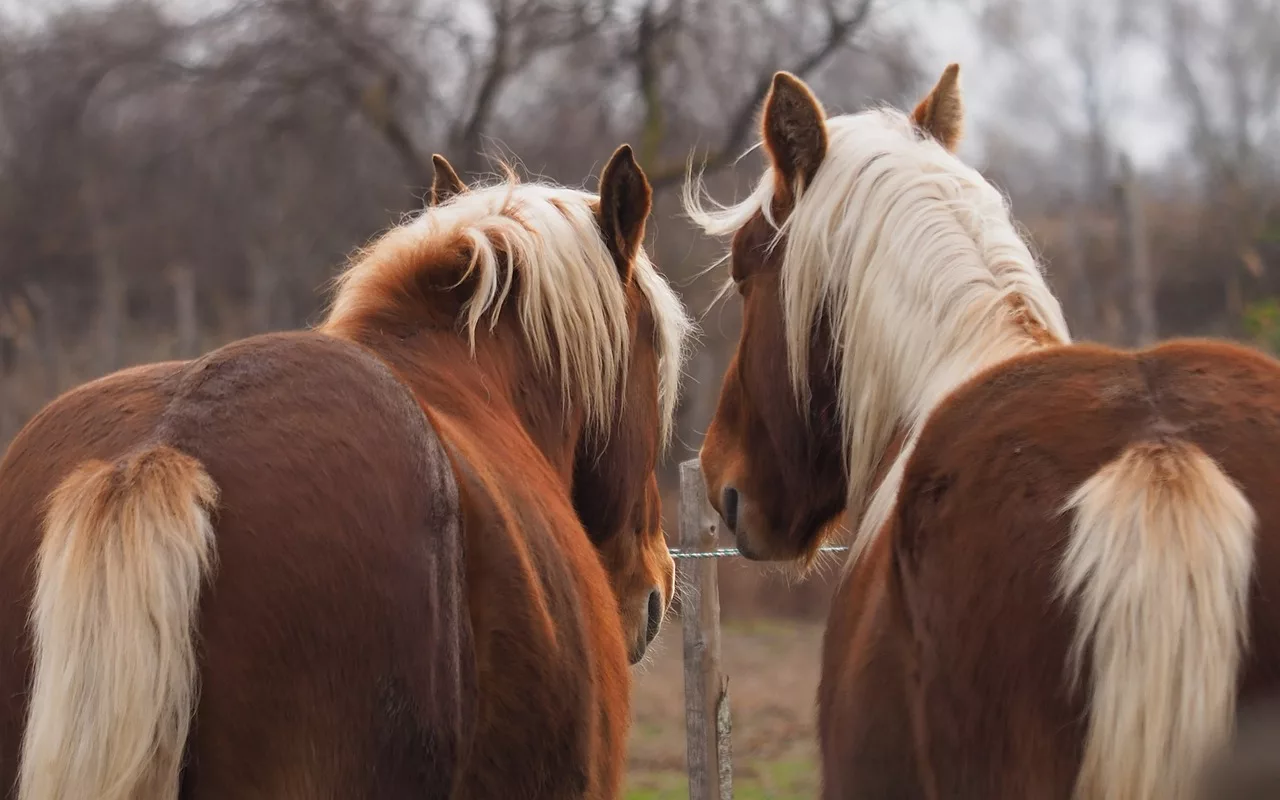
Only a handful of tanneries in the world are capable of producing shell cordovan from raw horsehide to the finished product. Among these are Rocado and Maryam in Italy, Shinki Hikaku in Japan, and the Horween Leather Company in the USA.
Founded in 1905 by Ukrainian immigrant Isadore Horween, the Horween Leather Company is one of the oldest continuously running tanneries in North America. It remains based in Chicago, where a number of tanneries sprung up at the turn of the century, taking advantage of the proximity to the Chicago River and easy access to livestock from the Midwest. The city’s location as a transportation hub and its meatpacking industry fuelled the development of these tanneries along what became known as Tannery Row.
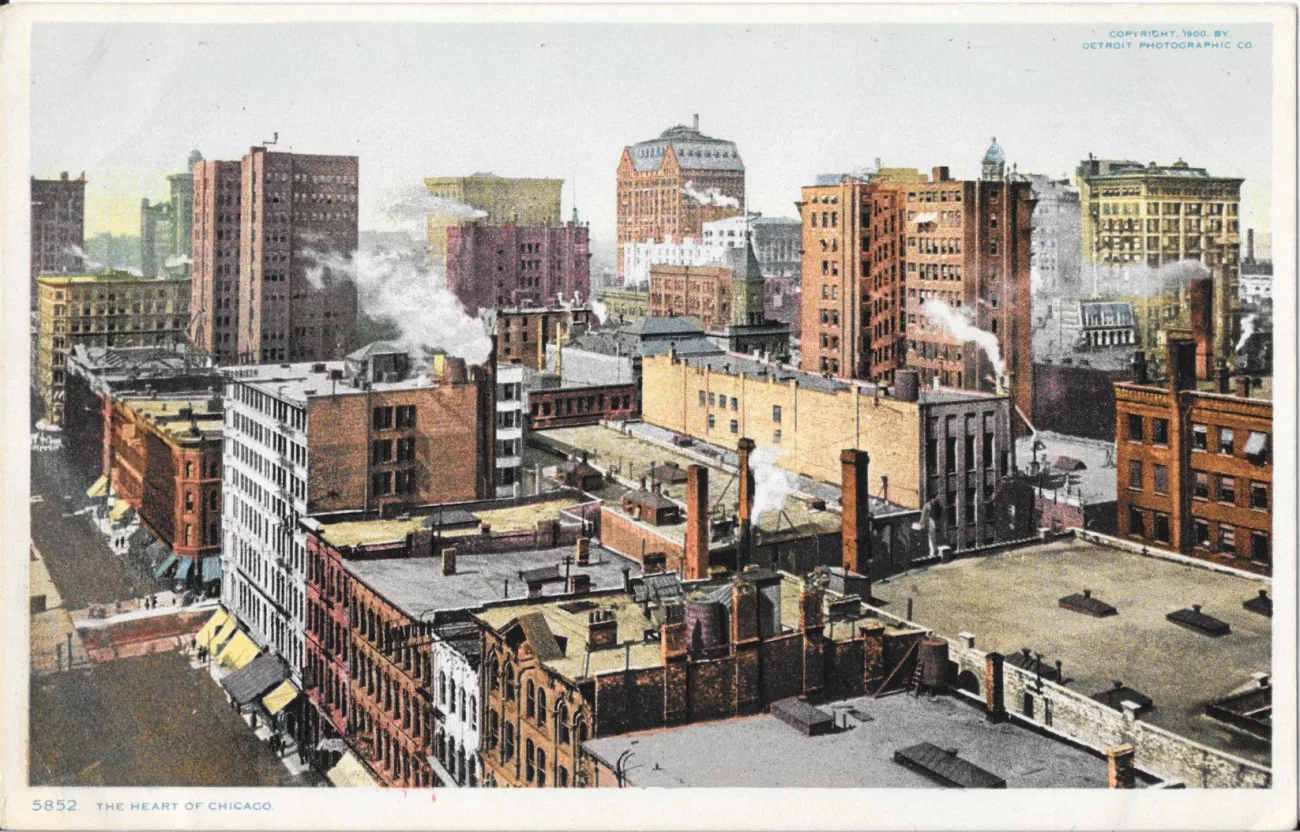
Isadore initially made only shell cordovan, which at the time was used primarily for sharpening strops for razors and other metal blades. The vegetable tanning process he developed is still used at Horween today and is a true testament to the family’s commitment to craftsmanship.
During tanning, the hides soak in large vats for sixty days – a time consuming process considering that modern chrome tanning can be completed in a single day. The recipe for the tanning solution remains the same as the one Isadore created more than a hundred years ago.
The skins then get hot stuffed with another family recipe of raw oils, waxes, and greases. Additionally, Horween curries the leather – a painstaking hand oiling process done one skin at a time by one man and his brush. After this, the skins are piled and left to age for another ninety days, before they are shaved to expose the super tight natural fibre structure which is the shell. As the shell is never at the same depth in different skins, and even at different depths in the same skin, it requires a highly skilled craftsman.
Multiple stain coats are applied to the shell which is left to dry naturally. It is then hand waxed and surface polished on a glazing jack which uses a smooth piece of glass to bring out the characteristic cordovan sheen.
Shell cordovan is used to make a variety of luxury items, such as bags, watch straps, and wallets, but it is perhaps most famous for its long tradition in shoemaking. The Italians were among the first to recognise this potential market in the early 20th century, when they began to make high-end shoes from shell cordovan for the fashion elite. Due to the material’s incredible strength and durability, a pair of shell cordovan shoes, if cared for properly, can last for decades.
In a world where fast fashion dominates, and many of the things we buy are destined for the bin, it’s worth thinking about what materials go into the products we consume. Sometimes less is truly more.